Both the engineered roughness and the hydrodynamic profile are innovations in the hydraulic design of bridges.
The engineered roughness in a golf ball allows it to travel about twice the distance that a smooth one, with the same size and mass, would attain with a same intensity blow. The Fluid Mechanics explains this so-called “golf ball effect” with the boundary layer concept. This thin layer that travels in contact with the rough ball’s surface detaches from the ball further downstream than in the smooth ball, and so the vorticose wake behind the golf ball is weaker and narrower.
Similarly, the rough bridge pier produces less scour, due to the diminished vorticity induced by the structure. Additionally, directional roughness in the upstream end of the Pier Sheath dampens the vertically directed secondary flow that powers the “horseshoe” vortex, main local scour mechanism (Fig. 1).
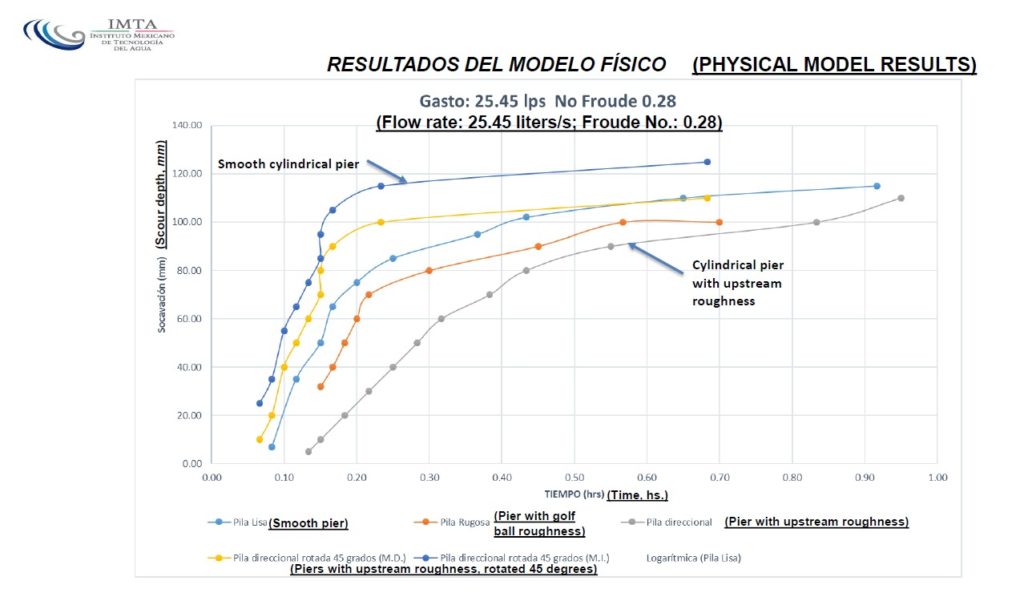
The advantageous flow around a hydrodynamic profile (with a minimum of wake vortices) is very well known, but the key hurdle involved in using it in submerged structures lies in the practical aspects of construction (forming, rebar), therefore it is not used; instead, blunt profiles are the norm. The Pier Sheath, a streamlined 3D-printed or precast add-on that can be installed around a common blunt bridge pier, solves this problem in a very efficient, convenient and permanent way.
The vorticity reduction means minimal local and wake vortex scour.
Another favorable effect of the Pier Sheath: due to the reduced momentum of the local scour mechanisms, the scour begins later in the flood timeline, progresses at a slower rate, and stops sooner, compared with a conventional pier. This increases the adaptive capacity and the resilience of the bridge against scour.